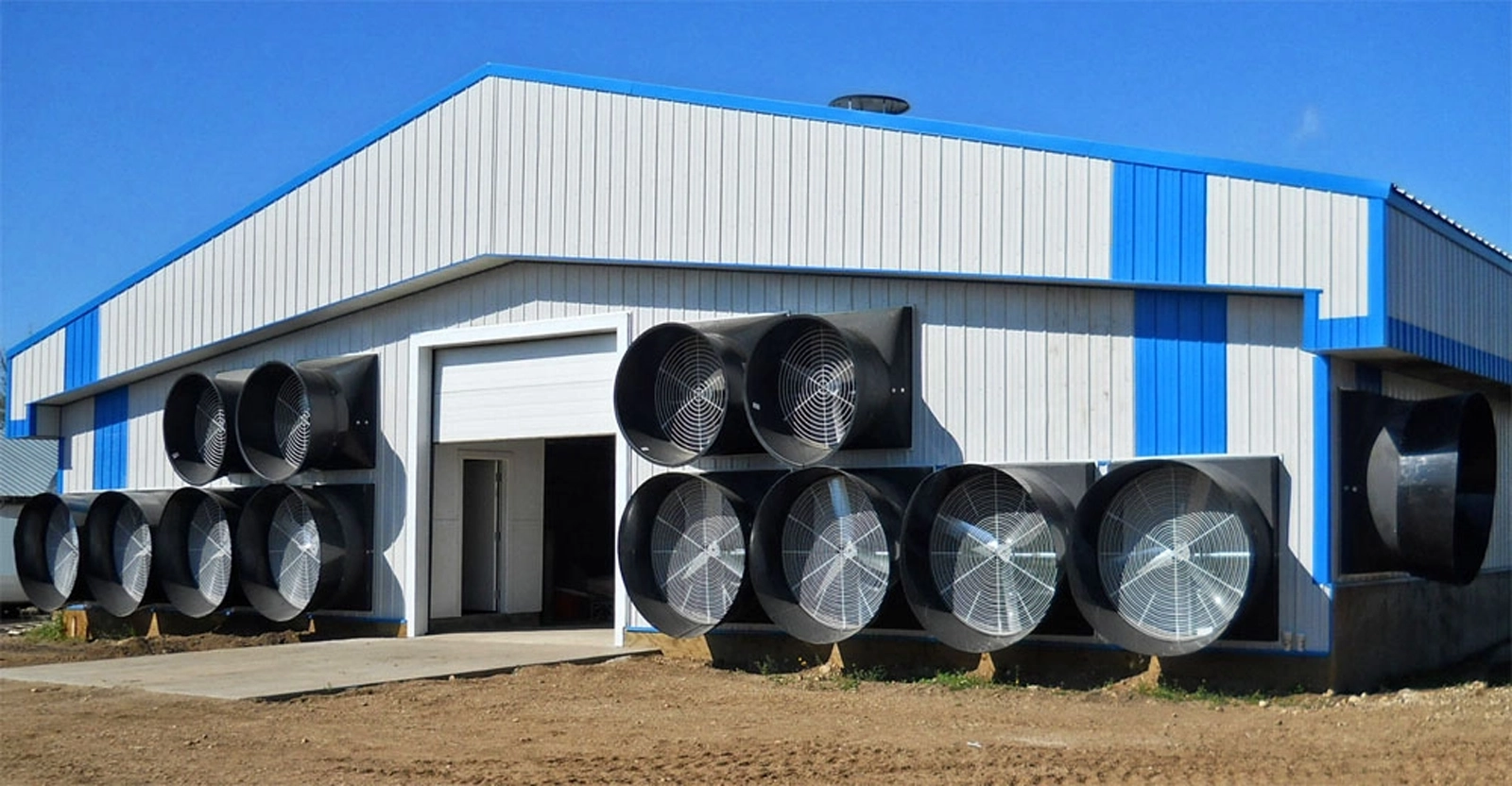
Proper barn ventilation is critical for ensuring optimal climate conditions and air quality in livestock facilities. Whether you manage a small, single-barn farm or a, multiunit livestock facility, sufficient ventilation is critical for livestock health. Farmers can create conditions that support the health, comfort, and performance of their animals by using a strategic combination of passive and active ventilation, helping ensure the long-term success of their agricultural enterprises.
Introduction to ECM fans
ECM is an abbreviation for “electronically commutated motor”. ECM motors are relatively new technology compared to the standard PSC (permanent split capacitor) motors. Whereas PSC motor technology is over 100 years old, ECM motors were introduced by General Electric in 1985.
ECM motors are known for their energy efficiency and precise control capabilities. With their ability to operate optimally at variable speeds and their permanent magnet design, ECM motors offer superior efficiency compared to other types of motors. ECM motors are used in various applications where precise control and energy efficiency are essential. Overall, ECM motors represent a significant advancement in motor technology.
How ECM motors work
ECM motors contain magnets that produce a steady magnetic field. When electricity is applied to the motor, it interacts with the magnetic field and causes the motor to spin. Because ECM motors do not do not need energy to generate a magnetic field, they are more efficient than PSC motors.
ECM motors are 10 to 20 percent more efficient at full speed than conventional induction motors, such as PSC motors, are. The increase in efficiency is noticed even more at slower speeds. Conventional motors become less efficient at slower speeds. ECM motors, on the other hand, have the same efficiency at all speeds. ECM motors are 30 percent or more efficient than conventional motors at slower speeds.
ECM motors rely on electronic controls and internal microprocessors to manage the flow of current to their motor windings. This precise control enables customized adjustments to the motor’s speed and torque, ensuring efficient operation across a broad range of speeds.
The internal microprocessor is critical for maintaining steady airflow. Using its factory programming and adjustable control board dip switches, the microprocessor maintains constant torque and airflow (measured in CFM) as the motor’s RPM adjusts to accommodate system conditions.
Torque variations within ECM motors are triggered by fluctuations in static pressure within the system. For example, higher temperatures or a clogged filter can raise static pressure, leading to an increase in motor torque. When the microprocessor detects an increase in torque, it immediately increases the motor speed to offset the resistance. The increase in speed not only maintains constant airflow but also reduces static pressure and torque.
During times of high demand, ECM motors deliver increased airflow for enhanced ventilation and cooling. It is important to calibrate the control board dip switch settings accurately to adapt to seasonal changes in ventilation needs, ensuring ECM motors operate optimally across different environmental conditions.
ECM motors, controlled by internal microprocessors, regulate torque, airflow, and speed precisely. Unlike standard motors, ECM motors cannot be field-programmed, emphasizing the importance of precise factory programming tailored to specific usage scenarios.
Advantages
- ECM motors are highly efficient, ranging from 65 to 75 percent depending on the output, resulting in reduced energy expenses.
- ECM motors provide increased efficiency, precise airflow selection (variable speed) in fans, and maintain consistent airflow during changes in system static pressure (constant airflow).
- ECM motors offer a broader operating range compared to typical induction motors, such as PSC motors, allowing a single ECM fan to replace multiple induction fans.
- ECM motors require less maintenance and are not prone to overheating compared to other types.
- ECM motors have a speed range of 0 to 100 percent. Speed adjustments can be permanently programmed into the motor or initiated by the controller when needed.
Drawbacks
- ECM motors are programmed at the factory, so they cannot easily be switched out with a new one off the shelf.
- ECM fans are more costly than regular fans.
- Repairs are more complex and specialized, and replacement parts may be more expensive.
- Installing and maintaining ECM fans may require specialized knowledge, which could mean training or hiring technicians familiar with ECM technology.
Controlling ECM fans
A major difference between ECM fans and PSC fans is that ECM fans can be controlled by a DC signal. For basic control, Phason’s Single Stage Variable DC Controller (FC-1T-1VDC) has a 0 to 10 VDC signal output and a disconnect relay that allows you to easily and effectively control ECM fans. The FC-1T-1VDC can control up to 10 ECM motors.
When the fans need to operate, the relay contacts are closed and the control provides a DC signal ranging from 0 to 10 V to the ECM motor, When the signal voltage is lower, the fan turns slowly. As the voltage increases, fan speed increases. When no ventilation is required, the relay contacts are open to ensure that there is no signal or voltage going to the fan.
Conclusion
Proper ventilation is critical for ensuring ideal climate and air quality in livestock facilities. ECM fans and motors represent a significant improvement in fan technology and provide energy-efficient, enhanced performance but, factors such as factory programming and higher startup costs must be considered as well.
If you need a more-advanced controller, the Touch Series and AutoFlex Connect offer the capability to control multiple rooms, and in the case of AutoFlex Connect, have remote connectivity. For more information about AutoFlex Connect and Supra Touch, visit their respective pages.